As someone who's been immersed in the manufacturing industry for over a decade, I've had the privilege of witnessing the evolution of precision components firsthand. However, nothing quite prepared me for the revelation that is brass CNC components from Vietnam. The first time I held one of these masterpieces, I was struck by more than just its physical attributes. It was a tangible representation of Vietnam's journey towards manufacturing excellence - a journey I've been fortunate enough to observe and participate in.
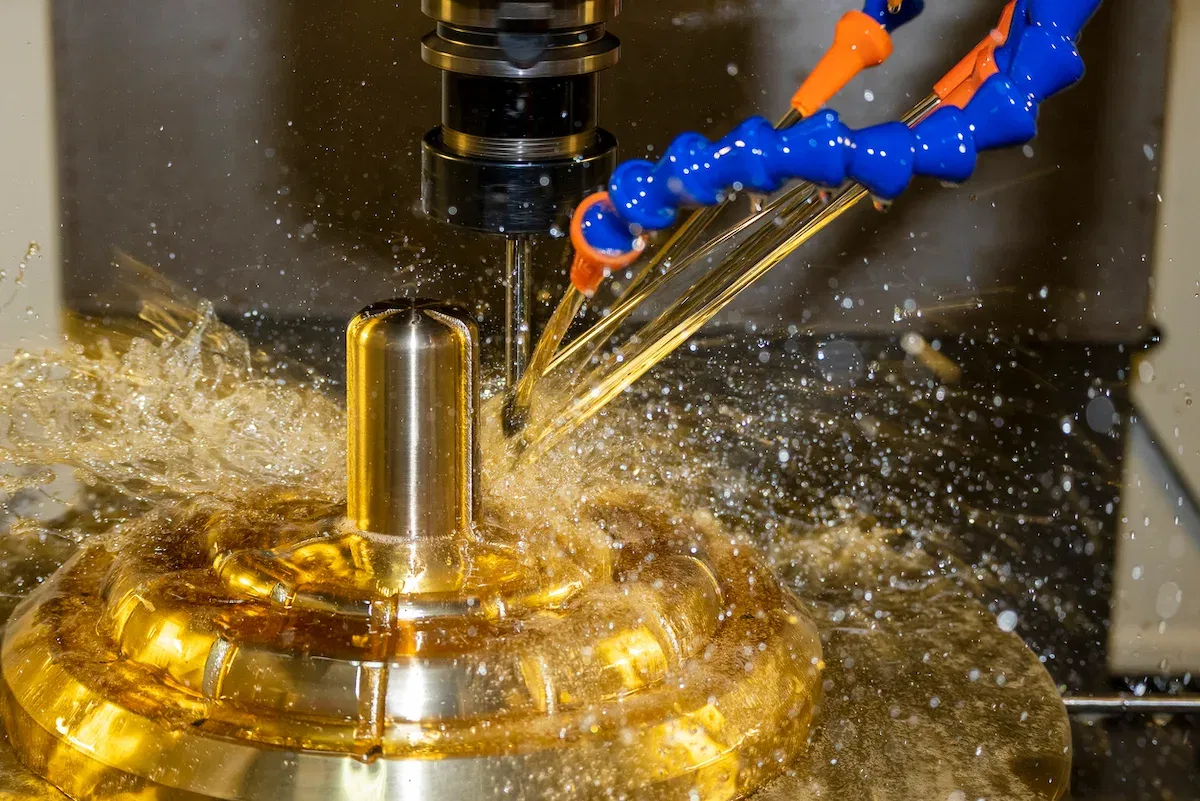
The Vietnamese Manufacturing Renaissance
Vietnam's rise in the world of precision manufacturing didn't happen overnight. It's been a carefully orchestrated symphony of technological adoption, skill development, and an unwavering commitment to quality. I've watched as small workshops transformed into state-of-the-art facilities, equipped with the latest CNC machines and staffed by highly skilled machinists, which contributes to making Vietnam a highly affordable location to manufacture CNC parts.
This transformation hasn't gone unnoticed by the global manufacturing community. According to a report by the Vietnam Association of Mechanical Industry, the country's mechanical engineering sector has been growing at an average rate of 16.5% annually over the past five years. This growth is particularly evident in the CNC machining subsector, where investments in advanced technology have skyrocketed.
The Brass Advantage
Why brass? It's a question I'm often asked, and the answer lies in the unique properties of this versatile alloy. Brass, typically composed of copper and zinc, offers a combination of characteristics that make it ideal for precision components:
-
Machinability: Brass is renowned for its excellent machinability. It can be cut, drilled, and shaped with ease, allowing for intricate designs and tight tolerances.
-
Corrosion Resistance: Unlike many metals, brass forms a protective layer when exposed to air, enhancing its resistance to corrosion.
-
Conductivity: Brass is an excellent conductor of both heat and electricity, making it suitable for a wide range of applications.
-
Strength: Although not as light as titanium, depending on the specific alloy, brass can offer impressive strength-to-weight ratios.
-
Aesthetics: The warm, golden hue of brass adds a touch of elegance to components, making it popular in decorative applications as well.
These properties, combined with Vietnam's advanced CNC machining capabilities, create a synergy that's hard to match. I've seen firsthand how this combination has led to components that not only meet but often exceed international standards.
Technical Marvels: Vietnamese CNC Capabilities
The CNC machining landscape in Vietnam is a far cry from what it was a decade ago. Today, it's not uncommon to find facilities equipped with 5-axis CNC machines capable of producing components with tolerances as tight as ±0.005mm. This level of precision is crucial in industries like aerospace and medical devices, where even the slightest deviation can have serious consequences.
One of the most impressive advancements I've witnessed is in the field of multi-tasking machines. These CNC marvels can perform turning, and milling operations in a single setup. The implications for productivity and accuracy are profound. I recently visited a facility in Ho Chi Minh City where a single multi-tasking machine was producing complex brass components that previously required three separate machines and multiple setups.
Case Study: Precision in Action
To illustrate the capabilities of Vietnamese brass CNC machining, let me share a recent project I was involved with. A European medical device manufacturer approached us with a challenging component - a brass micro-fluidic chip with channels as small as 50 microns. The tolerances were incredibly tight, and the surface finish requirements were stringent.
The Vietnamese team tackled the challenge head-on. They employed a combination of high-speed machining and micro-milling techniques, using tools as small as 0.1mm in diameter. The result was nothing short of spectacular. Not only did they meet the required tolerances, but they also achieved a surface roughness of Ra 0.2 μm, exceeding the client's expectations.
This project is just one example of many where Vietnamese manufacturers have proven their ability to compete at the highest levels of precision manufacturing.
Industry Applications: Where Brass CNC Shines
The versatility of brass CNC components from Vietnam has led to their adoption across a wide range of industries. Here are some key areas where I've seen significant impact:
Aerospace
In the aerospace industry, where safety and reliability are paramount, brass CNC components have found numerous applications. From hydraulic fittings to electrical connectors, these components play crucial roles in aircraft systems.
One aerospace client I worked with recently switched to Vietnamese-made brass components for their fuel management systems. The decision was driven by the need for parts that could withstand extreme temperature variations and resist corrosion. The results were impressive - a 15% reduction in component failures and a significant improvement in system reliability.
Medical Devices
The medical device industry demands components with uncompromising precision and biocompatibility. Brass, particularly alloys like C360 Free-Cutting Brass, has become a go-to material for many applications.
I recently toured a facility in Hanoi specializing in dental implant components. The precision of their brass CNC machined parts was astounding. They were producing threaded implant abutments with tolerances of ±0.01mm, ensuring a perfect fit and optimal patient outcomes.
Automotive
The automotive industry has long been a major consumer of brass components, and the shift towards electric vehicles has only increased this demand. Brass's excellent electrical conductivity makes it ideal for high-current connectors and battery terminals.
A notable project I was involved with last year focused on developing brass components for EV charging systems. The Vietnamese manufacturer we partnered with was able to produce complex, high-precision parts that met stringent safety and performance standards while keeping costs competitive.
Electronics
In the fast-paced world of electronics, brass CNC components play a crucial role in ensuring reliable connections and efficient heat dissipation. I've seen an increasing trend of electronics manufacturers turning to Vietnam for their brass component needs.
One success story that stands out is a collaboration with a leading smartphone manufacturer. They were struggling with signal integrity issues in their high-frequency antennas. By switching to precision-machined brass components from a Vietnamese supplier, they were able to improve signal strength by 20% while reducing manufacturing costs.
The Vietnamese Advantage: Quality, Cost, and Innovation
What sets Vietnam apart in the world of brass CNC machining? In my experience, it's a combination of factors:
-
Skilled Workforce: Vietnam has invested heavily in technical education. The country produces over 300,000 engineering graduates annually, many of whom specialize in advanced manufacturing technologies.
-
Cost-Effectiveness: While maintaining high quality standards, Vietnamese manufacturers often offer more competitive pricing than their counterparts in more established manufacturing hubs.
-
Technological Investment: Many Vietnamese CNC machining facilities boast state-of-the-art equipment, often on par with or exceeding what you'd find in Western countries.
-
Quality Focus: ISO certification is becoming the norm rather than the exception. I've worked with numerous Vietnamese manufacturers who hold ISO 9001, ISO 13485, and even AS9100 certifications.
-
Innovation Culture: There's a palpable energy of innovation in Vietnam's manufacturing sector. I've been impressed by the willingness to embrace new technologies and techniques.
Environmental Considerations
It's worth noting that Vietnam's brass CNC industry is not just focused on economic growth; there's a growing emphasis on sustainability. Many manufacturers I've worked with are implementing eco-friendly practices, from recycling brass swarf to investing in energy-efficient machinery.
One facility I visited recently had implemented a closed-loop coolant system that reduced their water consumption by 80% while improving the quality of their machined components. It's initiatives like these that demonstrate Vietnam's commitment to responsible manufacturing.
Looking to the Future
As we look ahead, I'm excited about the potential for further advancements in Vietnam's brass CNC manufacturing capabilities. The integration of Industry 4.0 technologies, such as IoT-enabled machines and AI-driven quality control, is already underway in some of the more advanced facilities.
Moreover, there's a growing trend towards customization and small-batch production. Vietnamese manufacturers are adapting to this shift, offering flexible production capabilities that can accommodate both high-volume orders and specialized, low-volume runs.
Conclusion: A New Standard in Precision Manufacturing
In conclusion, brass CNC components from Vietnam represent more than just precision-machined parts; they're a testament to the country's emergence as a global manufacturing powerhouse. The combination of advanced technology, skilled craftsmanship, and a commitment to quality has positioned Vietnam as a leader in this specialized field.
For businesses looking to source high-quality brass CNC components, Vietnam offers an compelling proposition - world-class quality at competitive prices. As someone who has witnessed the growth and development of this industry firsthand, I can confidently say that Vietnamese manufacturers are not just meeting global standards; they're setting new ones.
Whether you're designing cutting-edge medical devices, developing next-generation electronics, or pushing the boundaries of aerospace technology, consider the precision and quality that brass CNC components from Vietnam can bring to your projects. In my experience, it's a decision you won't regret.
FAQs
What are the benefits of using brass for CNC components?
Brass offers a unique combination of properties that make it ideal for CNC machining:
-
Excellent Machinability: Brass is known for its ease of machining, allowing for complex geometries and fine details. In my experience, this translates to faster production times and lower tool wear, ultimately reducing costs.
-
Corrosion Resistance: Brass forms a protective oxide layer when exposed to air, providing excellent resistance to corrosion. I've seen brass components perform flawlessly in harsh environments where other materials would quickly degrade.
-
Electrical and Thermal Conductivity: Brass is an excellent conductor of both electricity and heat. This makes it ideal for components in electrical systems or applications requiring efficient heat transfer.
-
Strength and Durability: Depending on the specific alloy, brass can offer impressive strength-to-weight ratios. I've worked on projects where brass components outperformed steel in certain applications due to their combination of strength and corrosion resistance.
-
Aesthetic Appeal: The warm, golden color of brass adds a touch of elegance to components. In industries where appearance matters, such as luxury goods or high-end electronics, this can be a significant advantage.
-
Cost-Effectiveness: While not the cheapest metal, brass often offers a good balance of performance and cost. When considering the total lifecycle cost of a component, including maintenance and replacement, brass can be a very economical choice.
-
Antimicrobial Properties: Some brass alloys exhibit natural antimicrobial properties, making them suitable for applications in healthcare settings or public spaces where hygiene is a concern.
How does CNC machining enhance the precision of brass components?
CNC (Computer Numerical Control) machining significantly enhances the precision of brass components in several ways:
-
Consistency and Repeatability: CNC machines can produce identical parts with incredibly high accuracy, ensuring consistency across large production runs. I've seen facilities produce thousands of brass components with variations of less than 0.01mm between parts.
-
Complex Geometries: Multi-axis CNC machines can create intricate shapes and features that would be difficult or impossible with manual machining. This opens up new design possibilities for engineers and product designers.
-
Tight Tolerances: Modern CNC machines can achieve tolerances as tight as ±0.005mm or even tighter in some cases. This level of precision is crucial for components in industries like aerospace or medical devices.
-
Surface Finish: CNC machining can produce excellent surface finishes on brass, often eliminating the need for secondary finishing operations. I've seen brass components come off CNC machines with surface roughness values as low as Ra 0.2 μm.
-
Multi-Operation Capability: Advanced CNC machines can perform multiple operations (turning, milling, drilling, etc.) in a single setup, reducing the potential for errors that can occur when moving parts between machines.
-
Programmable Precision: CNC machines can be programmed to make minute adjustments to account for tool wear or thermal expansion, maintaining precision throughout long production runs.
-
3D Contouring: 5-axis CNC machines can create complex 3D contours with high precision, allowing for optimized designs that were previously impractical to manufacture.
What industries commonly use brass CNC components?
Brass CNC components find applications across a wide range of industries due to their versatile properties. Here are some key sectors where I've seen significant use of these components:
-
Plumbing and Hydraulics: Brass fittings, valves, and connectors are widely used due to their corrosion resistance and durability. I've worked with manufacturers producing precision brass components for high-pressure hydraulic systems used in construction equipment.
-
Electrical and Electronics: Brass is commonly used for electrical connectors, terminals, and switch components due to its excellent conductivity. In one project, we developed miniature brass connectors for a wearable medical device, leveraging the material's conductivity and biocompatibility.
-
Automotive: The automotive industry uses brass components in fuel systems, radiators, and electrical systems. With the rise of electric vehicles, I've seen increased demand for high-precision brass components in battery management systems and charging infrastructure.
-
Aerospace: Brass components are used in aircraft hydraulic systems, fuel management, and electrical systems. The material's combination of corrosion resistance and machinability makes it ideal for complex aerospace components.
-
Marine: In marine applications, brass is valued for its corrosion resistance in saltwater environments. I've been involved in projects developing brass components for marine engines and navigation equipment.
-
Medical Devices: Brass, particularly lead-free alloys, is used in various medical devices and surgical instruments. Its antimicrobial properties and precision machinability make it suitable for components in diagnostic equipment and implantable devices.
-
Telecommunications: The telecommunications industry uses brass components in antennas, waveguides, and other high-frequency applications. I've seen an increasing demand for precision brass components in 5G infrastructure equipment.
-
Oil and Gas: In the oil and gas industry, brass components are used in various instruments and control systems due to their corrosion resistance and reliability in harsh environments.
-
Instrumentation: Precision brass components are crucial in many scientific and measuring instruments. I've worked on projects developing brass components for high-accuracy pressure sensors and flow meters.
-
Robotics and Automation: As the robotics industry grows, so does the demand for precision brass components. These are used in actuators, sensors, and other critical systems where reliability and precision are paramount.